Power outages during cold weather events can be avoided. It can be done without the huge expense of winterizing a plant, especially in an area that very rarely sees extreme weather. Not only can the expense of winterizing be greatly reduced, but it can save operations money regardless of weather conditions. All of it is entirely possible with the use of a Sandwich Belt high angle conveyor.
Places that rarely experience extreme cold aren’t going to budget in the extreme expense of winterizing their operations. But after the record breaking Arctic freeze that swept the state of Texas, officials are now discussing the reality of an astronomical expense to prepare for another rare possibility of crippling winter weather.
There is a simple solution that absolutely should be considered by plants handling fuels – both fossil fuels and biofuels. Not only in Texas, but anywhere that has the potential for a weather event that can shut down operations. The foresight in the design of a Sandwich Belt high angle conveyor is a simple solution that can address the needs of these operations, but even more, save them money instead of creating expense.
ALREADY WINTERIZED
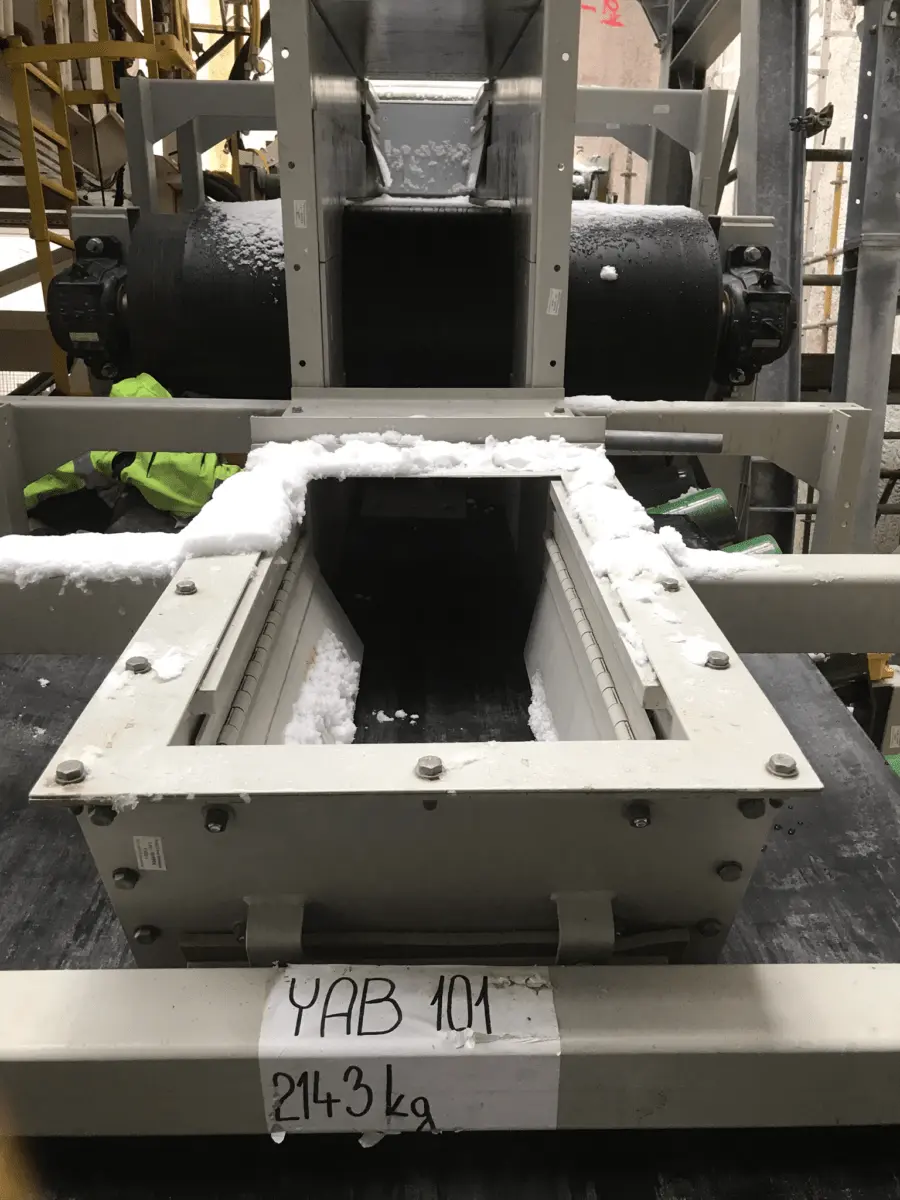
Many bulk materials used for power are stored in open piles until use. In extremely cold conditions, it can pose problems for these materials to be conveyed if they are covered in snow or even frozen. From wood chips, to coal, to biomass pellets, these commodities can be the life line to maintain electricity for millions of people in extreme weather conditions.
In some places, extreme cold is expected and plants have plans to winterize their operations for these seasons. However, if extreme weather conditions like snow and ice are rare, the expense of winterizing won’t be implemented.
Many plants are using conventional troughed conveyors. With these, if materials are frozen, they may have the tendency to slide back due to slick and slide of the frosted material on the frosted belt surface. When this happens, the solution tends to be to reduce the load size and/or reduce the belt speed. While logical solutions, these recommendations are costly as they slow down operations and reduce throughput. Even worse, when faced with a situation of an unexpected Arctic freeze in areas that do not typically experience these conditions, this can be detrimental to maintaining power in a dire situation.
While the recommendations to scale back operations seems logical, it’s made without the consideration of Sandwich Belt high angle conveyors. Sandwich Belt high angle conveyors don’t only save money, but they are designed to take on the rugged conditions in any climate and alleviate the expense for winterizing.
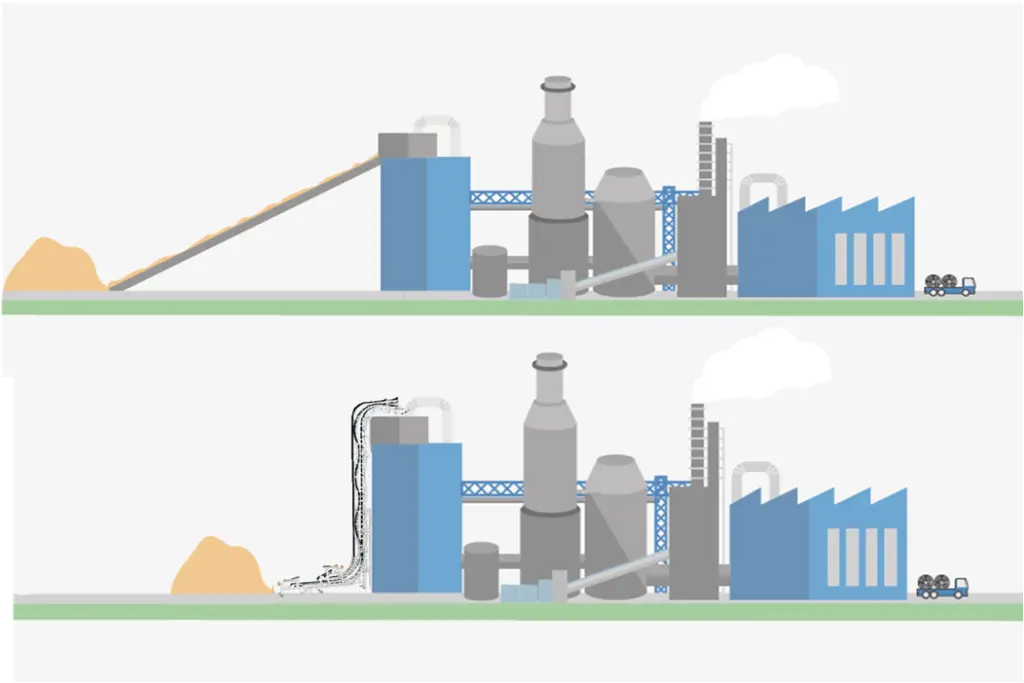
REDUCED FOOTPRINT
Reduction of the conveyor slope creates an added expense for operations. Aside from the additional real estate, it may require covers around the low angled conveyor system, or even a large building enclosure depending on how extreme temperatures get.
With Sandwich Belt high angle conveyors, the ability to convey at a higher angle not only saves on real estate, but offers a more cost effective means of housing the conveyor system within a smaller, heated building.
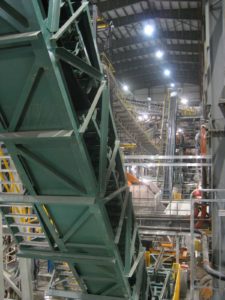
Such was the case for five Sandwich Belt conveyors that were installed for the DeBeers diamond mines in Canada. Because of the hostile environment, the facilities had to be enclosed and heated. The smaller footprint for the plant was determined to be the optimal way to minimize environmental impact and cost. This led to pursuit of the Sandwich Belt high angle conveyor because of its space saving features.
If enclosing the conveyor system is not an option, the Sandwich Belt high angle conveyor still has advantages that do not require a slowdown of operations or added expense.
Because material is gently hugged between the two belts, it can still protect the product from the elements. This eliminates the need for covers along the conveyor path. It also eliminates the expense of spraying chemical solutions on the material to behave a certain way to be conveyed. These chemical solutions can additionally have adverse effects on the environment. The Sandwich Belt conveyor takes the material as is and conveys it gently and efficiently. Any sticking to the belt is thwarted with belt scrapers at the head end.
Additionally, there is no concern that frozen material will roll back or that wind gusts would blow vulnerable product off the belt as would occur on a lower angled open troughed belt.
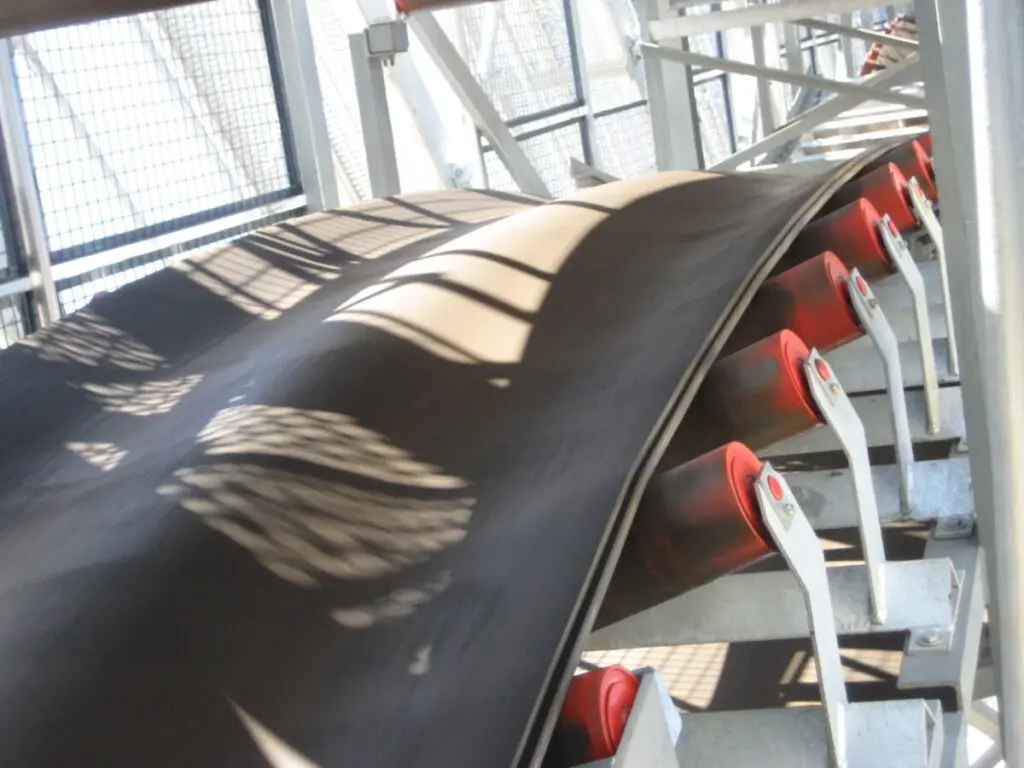
MAINTENANCE
Maintenance is necessary at any plant. It was reported that a scheduled shut down in Texas was happening when the winter storm hit. The unfortunate coincidence may have cost precious time in being able to restore power. Fortunately, a Sandwich Belt high angle conveyor is made of all conventional conveyor parts, so there is no concern for extra delays. The maintenance that occurs with any conventional conveyor remains the same with a Sandwich Belt conveyor.
PROVEN AND RELIABLE
Sandwich Belt high angle conveyors have found wide use in the marketplace around the world. They have proven to be versatile with widely varying applications, along with the benefit of environmental considerations. While plants in Texas tackle the next phase of winterizing their operations, it should be done with the consideration of a Sandwich Belt high angle conveyor.