ORIGIN OF THE SANDWICH BELT HIGH ANGLE CONVEYOR
In 1979 Joseph A. Dos Santos undertook a major study to develop a means of moving and elevating large quantities of bulk materials, including coarse products such as rocks, aggregate, coal, etc. at the steepest possible inclines.
It was also his intent to use only existing and generally available hardware in order to achieve the most economically feasible and easily maintained high angle conveyor design.
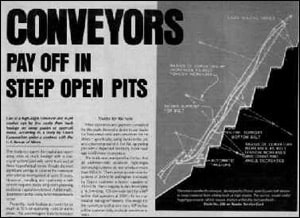
Mr. Dos Santos conceived, researched and developed his sandwich belt design, with the help of a grant from the U.S. Bureau of Mines, while he was employed by a major American manufacturer of materials handling equipment. While such concepts had been tried over the years with mixed results, Dos Santos investigated & analyzed the many forces generated in this seemingly simple concept, and created the formulas which guaranteed the successful design of such equipment. The DSI Snake Sandwich Conveyor represents the ultimate achievement of this aim.
Mr. Dos Santos’ research articles have been published in world-wide journals.
What is a Sandwich Belt High Angle Conveyor?
A Sandwich Belt conveyor uses two conveyor belts, face-to-face, to gently but firmly contain the product being carried, hence making steep incline and even vertical-lift runs easily achievable.
What Sandwich belt high angle conveyor profiles are available?
DSI Snake Sandwich Belt Conveyors are available in widely ranging profiles of C and S-Shape. In any case, a long bottom belt approach is possible to the sandwich entrance, and discharge may be on the high incline or may be after the extension of the carrying belt beyond the mouth of the sandwich.
FREQUENTLY ASKED QUESTIONS
No, the Sandwich Belt high angle conveyor is not a new technology. In fact, the actual development of the sandwich belt high angle conveyor technology by J.A. Dos Santos, founder of Dos Santos International, occurred between 1979 and 1982. During this period Dos Santos developed several variations of the system including the Sandwich Belt High Angle Conveyor and a mechanically pressed system using fully equalized pressure rolls. The former, the preferred system, was submitted to the patent office in 1980. From 1982 to 1997, he refined the latter concept into the HAC® and was awarded three USA and foreign patents on the system. J.A. Dos Santos is the author of all of the design standards for this system and has published extensively on the subject. He had installed more than eighty commercial systems by 1997.
Since the founding of DSI in 1997, many DSI Sandwich Belt High Angle Conveyors have been supplied across a wide range of industries. This installation list continues to grow.
All of these systems are capability of conveying at high angles, but the distinct difference in these and the advantages of Sandwich Belth high angle conveyors are outlined below.
Molded Cleat Belts
- The cleats will wear more rapidly than the standard smooth top cover of the sandwich belt, and the cleated belt may lose its inclined conveying capabilities.
- At high belt speeds, as the cleats pass over the return rollers, vibrations can occur that cause accelerated cleat wear and a reduction in return roll bearing life.
- The cleated belt is more difficult to clean than standard conveyor belt.
- Belt brushes, belt beaters, air blasters, water sprays or a wash box belt cleaner must be used.
- Molded cleat belts are usually restricted to short conveyors where few or no return idlers are needed and either the material does not stick to the surface or where material carry back is acceptable.
Pocket Belts
- The pocket belt is more expensive than standard conveyor belting.
- Lump size is somewhat limited particularly at high angles of incline as the pocket belt capacity is determined by the profile of the pocket.
- Sidewalls and cleats are susceptible to damage.
- Belt training must be maintained accurately to reduce damage to the sidewalls.
- The belt is more difficult to clean than standard conveyor belts. Belt beaters, air knives, water sprays or a wash trough must be used.
Bucket Elevators
- Carry back and spillage.
Lower capacity and increased power consumption. - High wear and noise level.
- High maintenance and specialty replacement parts.
DSI Sandwich Belt High Angle Conveyor Advantages over the others
- Unlimited conveying capacity.
- A system suitable for the most rugged mine applications, yet gentle on sensitive and friable materials.
- High availability and low operating and maintenance cost.
- Smooth surfaced belts allow continuous belt cleaning by scrapers and plows.
- Facilitates intermediate material discharge by belt plows, as appropriate, before and/or beyond the sandwiched part of the snaking profile.
- All conventional conveyor hardware ensures economy and fast delivery of replacement parts.
No, the DSI Sandwich Belt High Angle Conveyor is very low maintenance, requiring the same or less effort than conventional conveyors operating in the same capacity. At several of the units we’ve visited in the past, plant managers and those working directly with the conveyor system say the same thing. Plant operators have advised that they wish they had Sandwich Belt High Angle Conveyors all over their plant, as the frequency of maintenance on the other conveyors were more likely to cause production losses. Finally, the DSI Sandwich Belt High Angle Conveyor is made up of all conventional conveyor parts, so it ensures economy and fast delivery of replacement parts.
You’d be surprised at the astonished looks we’ve received at a start up of a DSI Sandwich Belt High Angle Conveyor, or the many questions even fabricators will ask, including “How is this conveyor system going to work?” Seeing is believing, and often times, these doubters become a great promoters for the product, testifying to the success and reliability of the DSI Sandwich Belt High Angle Conveyor.
A sandwich belt conveyor uses two conveyor belts, face-to-face, to gently but firmly contain the product being carried, hence making steep incline and even vertical-lift runs easily achievable. The DSI Snake hugs the bulk materials by the use of radial pressure which is due to the belt tension and the alternating curving profile geometry. Materials are conveyed along the convex curves in a “snaking” profile as they are elevated to the highest of angles.
The HAC® technology is built from the same basis as the Sandwich Belt Conveyor (see Point 1 above.) Other forms of high angle conveying (pocket belts, bucket elevators, etc.) are not often regarded as real competitors to the Sandwich Belt High Angle Conveyor, due to their lack of capabilities as compared to the Sandwich Belt High Angle Conveyor (see Point 2 above.) On the other hand, the HAC®, which was developed by J.A. Dos Santos employs the same inherent technology, with one primary difference. The full story follows:
Background
The actual development of the Sandwich belt high angle conveyor technology by J.A. Dos Santos occurred between 1979 and 1982. During this time, Dos Santos developed several variations of the system including the Snake Sandwich High Angle Conveyor and a mechanically pressed system using fully equalized pressure rolls. The former, the preferred system, was submitted to the patent office in 1980. In 1982, J.A. Dos Santos joined Continental Conveyor of Winfield, Alabama USA (now Joy Global.) During the period 1982 to 1997, he refined the mechanically pressed concept into the HAC® and was awarded three USA and foreign patents on the system. The difference between the DSI Sandwich Belt High Angle Conveyor and HAC® is that the HAC® employs special pressing mechanisms with fully equalized pressing rolls, to hug the material as its being elevated. The DSI Sandwich Belt High Angle Conveyor technology conveys materials along a series of alternating convex curves, developing radial hugging pressure through tension. The HAC® remains a successful elevating system and DSI also offers our advanced version of the HAC®, which we have dubbed the GPS, or Gently Pressed Sandwich. The key point to remember is the J.A. Dos Santos, founder of Dos Santos International is the developer of the Sandwich Belt High Angle Conveyor and the HAC®/GPS. He is the mind behind the machine, and he has imparted his expertise onto all DSI personnel, making DSI the unparalleled leader in all forms of sandwich belt high angle conveying. No one on earth knows these conveying systems better.
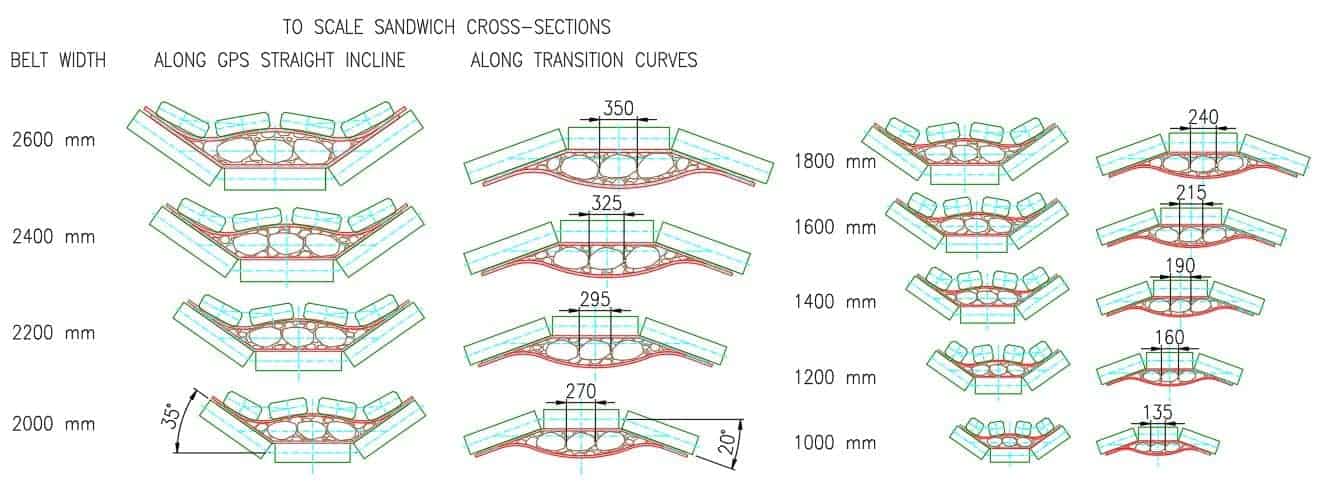
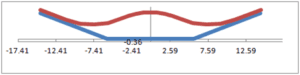
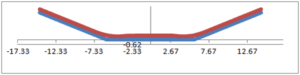
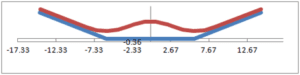
While we promote our high angle conveyors most prominently, we also are very experienced throughout the materials handling field. In fact, we have developed a number of studies for mine expansions and new projects. Our primary focus in these studies has typically been conveying, but we have also offered input on storage arrangements and ship-loading dock layouts. Further, we remain busy offering our ExConTec analysis for plant and overland conveyors. This software allows us to offer full static and rigid boy dynamic analysis of the most complex conveyor systems, and thereby optimize design of a new conveyor, or rectify problem points on existing conveyors. Dos Santos International has engineered and supplied horizontally curving overland systems and mobile ship loaders. Dos Santos International offers over 30 years in materials handling and general consulting services.
Please contact us with any applications you may have and we will be happy to provide
you with a budget quote and our engineering expertise for your latest project.