Dos Santos International was awarded a contract near the Gulf of Mexico, which includes engineering support and supply of a DSI Snake Sandwich High Angle Conveyor – the widest belt width, highest volumetric rate DSI Snake to date.
Dos Santos International has long provided expert engineering support to a major transfer terminal on the Mississippi River delta, North American Gulf of Mexico. Barge tows of coal and coke from all over the USA travel south on the Mississippi River to the terminal where they are unloaded to storage. The stored material is later reclaimed and loaded into ships that deliver the coal and coke to power plants, steel mills and chemical plants, along the Gulf coast and all over the world. The terminal transfers 20 to 30 million tons annually.
BACKGROUND
When built in 1965, the terminal consisted of a bucket ladder type continuous barge unloader (CBU), a storage yard, served by a reversing yard belt with a bucket wheel type stacker reclaimer (S/R), and a slewing, luffing and telescoping type loader for Gulf barges and small ships. The main market was the power plants along the North American Gulf coast. Additional down river dock structure was later added along with the clamshell type unloading equipment to handle specialty materials.
International coal trade increased dramatically through the 1970’s. A major expansion of the terminal, in the early 1980’s sought to capitalize on the increased coal trade. A second, parallel, but higher capacity system was added just up-river from the first. The new system included a double bucket ladder, pivoted arm type continuous barge unloader (CBU), a storage yard served by a reversing yard belt with a bigger, higher capacity stacker reclaimer (S/R) and a new travelling, luffing, telescoping ship loader on a new dock structure between the two storage yards. The new travelling ship loader could easily load large ships. Parallel tripped conveyors at the new dock, one running up-river, the other down-river, allowed the ship loading of the coal from either yard. Other than sharing the common ship loader, the two storage yards remained isolated from each other depending entirely on the availability of their local equipment. At each stock yard it was not possible to simultaneously stack and reclaim.
A major expansion sought to end the isolation. Ahead of the expansion, the original S/R of the down river yard was replaced with a new, modern S/R with the increased operating parameters of the upstream system. The latest expansion included:
- An additional parallel reversing yard belt at each storage yard, served by the yard’s stacker reclaimer.
a. Either yard belt tripper can feed the S/R to stack-out.
b. In reclaim mode, the S/R can load either yard belt through a bifurcated chute with
actuated flop gate. - Two additional stackers at each yard; one on either side of the S/R:
a. Each stacker has a reversing boom conveyor that can stack to either side of the track.
b. Each stacker is loaded by either of its two yard belt trippers. - Up river and down river conveyors to direct material flow from either CBU to either storage
yard or from reclaiming at either yard to ship loading via either end of the main dock. - Three new slewing, telescoping ship loaders, located downriver of the main dock. These
new ship loaders, though stationary are designed with the combined operating range to
load large ships without re-positioning.
The isolation is ended with the new up-river and down-river conveyors that link the two storage yards. To preserve maximum stacking range along the yards the up/ down-river conveyors must hug the CBU dock line, locating them alternately over land and over water. The original yard belts are broken into two flights at the respective junctures with the up/ down-river conveyors. Thus, from either CBU, material flow can be alternately directed to either storage yard for stack out or directly to any of the ship loaders.
HIGH-TECH TRANSFERS
The expansion maximizes flexibility allowing continuous stack-out at either or both yards with simultaneous continuous reclaim to ship loading from either or both storage yards. This flow path flexibility is facilitated through elaborate junctures of high-tech control flow chutes, particularly at the ends of the new up/ down river conveyors. These transfers are contracted separately to the control flow specialists of Power Techniques of Alma, Illinois, USA and M & J Engineering of Germiston, South Africa. These control flow chutes are well known in the trade as Weba Chutes.
ENVIRONMENTAL AND OPERATION IMPROVEMENTS
The current expansion afforded the opportunity to establish better environmental controls and to better deal with nagging operational issues. These are related. Whereas conventional open troughed belt conveyors can ideally operate at inclines as high as 15° to 17°, practically, variations in material characteristics can greatly affect this, significantly lowering the incline angle.
Barged coal often arrives in very wet condition. The barges may have been loaded with wet coal and/ or the open barges may take on additional moisture from long exposure to downpours of rain.
In transit, excess water tends to gravitate to the bottom of the barge. When unloaded by the bucket ladder type CBU, the first “hogging” pass delivers a moist coal mix but the final pass drags the barge’s bottom and bails the excess water. In many cases such a wet material/free water mix cannot be conveyed at any significant incline and tends to run back, spilling from the conveyor.
Operational and design parameters for the terminal expansion were developed from such experience. As a result: 1) conveyor incline angles are limited to 9° throughout the terminal; 2) All new elevated conveyors are to have full length drip pans to catch any spillage so that wash-downcan direct it to a strategic collection point. These two mandates promise to improve the environment at and around the terminal.
DSI SNAKE, OPTIMAL PATH FROM THE DOWN RIVER CBU
The new system layout required a new conveying path from the down river CBU to the new down-river transfer complex. The direct path to discharge over the down river yard belts subtends an incline angle that far exceeds the capability of any conventional open troughed belt conveyor. The reflexive solution was to use two conventional conveyor flights in a switch-back arrangement. The 9° maximum incline limitation and the location over water made this a costly proposition. The large (environmental) footprint was also a negative.
Because of the long relationship with Dos Santos International, terminal personnel knew there was a better solution: a DSI Snake Sandwich High Angle Conveyor. At 3629 t/h (4000 STPH) of coal this would be the highest volumetric rate to date for a Dos Santos Sandwich Belt High Angle Conveyor. The Terminal management, in their due-diligence, sent key professionals to visit the operation of Dos Santos Sandwich units handling coal at high volumetric rates. These visits, and discussions with operating and maintenance personnel, confirmed that the DSI Snake was the best solution.
The DSI Snake was ordered in April of 2014 with operation to begin in early 2015. The new DSI Snake profile is depicted in Figure 1 along with the alternate conventional conveyor solution for contrast.
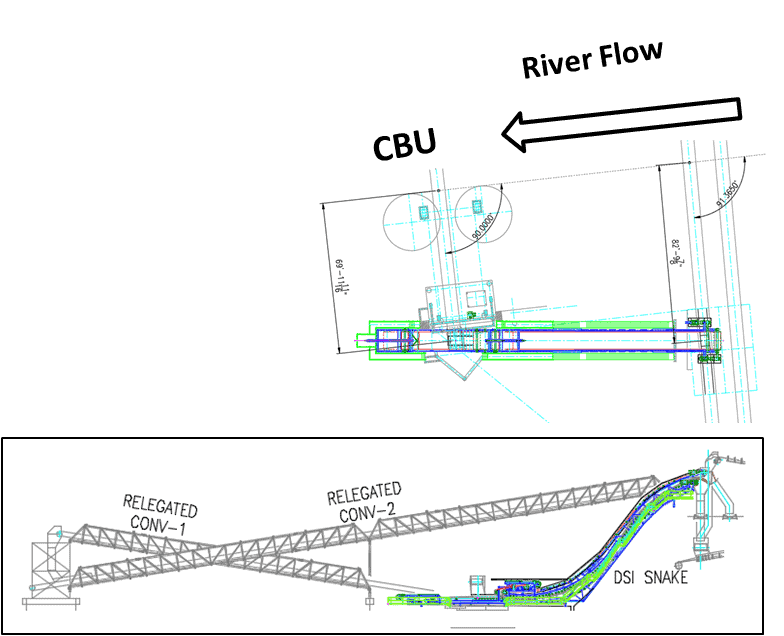
Figure 2 shows the Snake arrangement along with a summary of the design specifications and features. At 2438 mm (96”) of belt width this is the widest Dos Santos Sandwich Belt unit.
The Snake is part of the coal flow path from the original down-river CBU to the top of the new down-river transfer tower. The bucket ladder type CBU unloads the coal from the barges and discharges it onto the gathering “A” conveyor, which discharges to the connecting “B” conveyor. The DSI Snake receives the coal load from the B-conveyor discharge and elevates it continuously up to the transfer tower, for distribution to the alternate terminal destinations. The CBU travels up and down the support tower as required; to clear the empty barge at the highest river level and to dig into the fully loaded barge at the lowest river level. Thus the tail of the connecting B-conveyor follows the CBU travel while the head end pivots to the resulting incline angle. The material discharge onto the DSI Snake unit would vary accordingly.
Special features of the Snake include galvanized steel structure, corrugated covers and wind guard, and a full length stainless steel drip pan to a strategic discharge point at the foot of the inclined structure. Naturally, at 52° incline the drip pan will be self-cleaning. Additionally the bottom belt tail end is extended back, behind the loading area, in order to facilitate belt splicing.
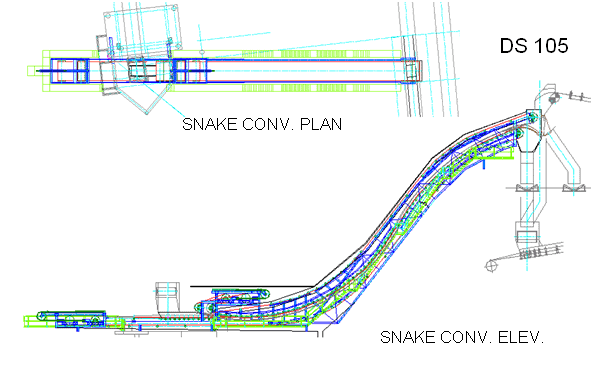
The lower end of the Snake would be largely supported on existing structure while the main incline structure will be supported on a new pile group at the bottom and on the new transfer tower at the top. A pair of smaller piles would support the bottom belt take-up area.
The DSI Snake Conveyor would be a substantial improvement over the switch-back conveyor arrangement originally conceived. Its use will eliminate a transfer, along with the substantial additional tower and foundations that would be required to support the switch-back transfer. Its shorter path and material containment will further limit the environmental impact of the material handling system. These, among other benefits of the DSI Snake, made this unit an ideal solution for this application.
Unfortunately, even after engineering and supply was completed, the terminal again went through major economic challenges and halted the installation of the DSI Snake. The equipment still remains at the site, with the hope that it will eventually be installed and greatly benefit the terminals operations.