Dos Santos International continues its legacy of innovation with the latest patented conveyor, the DSI TBM trailing Sandwich Belt high angle conveyor.
After many installations that received tunnel muck from conventional TBM trailing conveyors, beginning in 2019, Dos Santos developed the TBM trailing Sandwich Belt high angle trailing conveyor. Two USA patents were awarded to Dos Santos International. The first patent was awarded on October 19, 2021. A second patent that broadened the invention and expanded the claims was awarded on November 1, 2022. Joseph A. Dos Santos is the inventor. The invention is to haul bulk material away from continuous mining machines and, more particularly, from a TBM (tunnel boring machine) along any high angle incline.
In a typical mining operation such as tunneling, it is well known to use a continuous mining machine, such as a TBM, to advance the mine face continuously without interruption. The rock material or muck must be hauled away continuously from the face. The conventional, open troughed extendable trailing conveyor has traditionally fulfilled this function as typical tunnel excavations are not along steep inclines.
Occasionally a tunnel must be excavated along a steep incline exceeding 15 to 18 °. A TBM is capable of such steep excavation, but the traditional open trough conveyor cannot serve the muck clearance function as the muck would slide
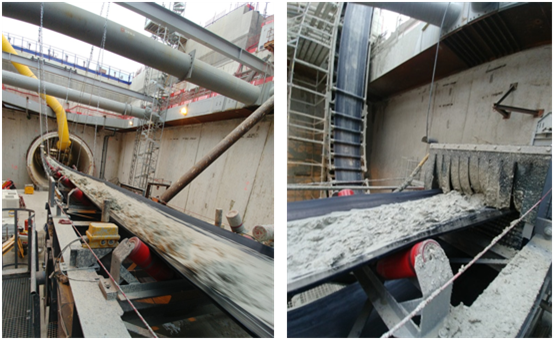
down on the belt at such angles. Dos Santos Sandwich Belt high angle conveyors are well developed and well known to have the operating characteristics of conventional open trough conveyors but they also have the capability of conveying the bulk at any high angle. This is done by sandwiching the bulk between two belts, hugging the material continuously (without lapse) in order to develop its internal friction which resists any tendency to slide down. The DSI invention extends the high angle capability to the TBM trailing conveyor.
In 2019, the challenge was presented to Dos Santos International. A major tunneling project in Australia required the excavation to begin along a horizontal path then to increase in slope to 25°. The 25° slope continued 1163 meters then again reduced to a lower, near horizontal angle along the remainder of the tunnel. DSI embraced the challenge. Some key elements of the invention were determined in the requirements of this project but not all. The requirements are summarized:
- The TBM trailing conveyor system must begin at the launch of the TBM and must continue to haul the muck to the discharge point that is established at the launch.
- The loading point must be on the TBM trailing deck.
- The system must extend in length while in operation as the TBM advances the tunnel excavation.
- This requires a belt storage unit at the launch for both the top belt and for the bottom belt of the Sandwich conveyor.
- This also requires that conveyor structure is added safely at the tunnel, from the TBM trailing deck as the Trailing Sandwich conveyor extends with advance of the excavation.

Whereas the use of the belt storage units (one at each belt) is relatively straightforward, as is the loading at the TBM trailing deck, the transition from the low loading angle (onto the bottom belt) to the sandwich, then to the high angle is not. Indeed, it is unprecedented.
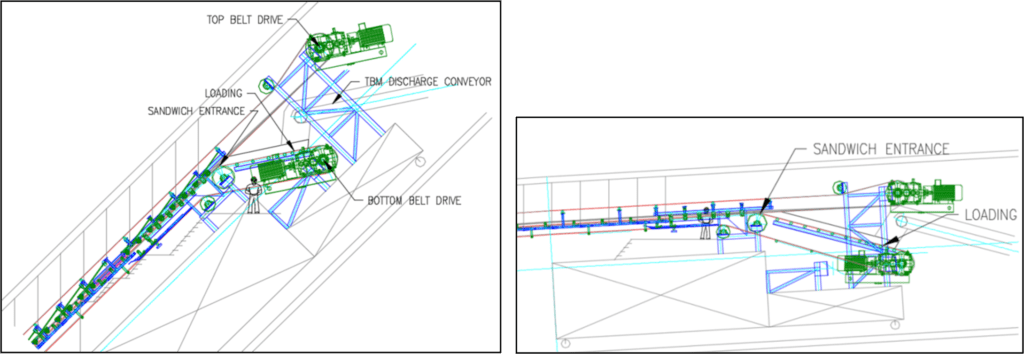
Traditionally the transition from the sandwich entrance to the high angle has been gradual along a troughed convex transition curve. Such a curve is not possible within the space of the straight tunnel. The transition is thus abrupt. The skirted, flat bottom belt with the bulk load travels into the sandwich over a large diameter bend pulley that immediately deflects the belt line to the high angle. The top belt joins the bottom belt at the high incline covering the material stream immediately, imposing only a gentle hugging pressure onto the bulk material.
The challenge of the 2019 Australian project inquiry prompted the invention, but vision of the broader requirements, including much higher tunnel angles, formed the basis for the broader invention.
Most challenging of the broader higher angle requirements is the need for an interim hugging pressure as the permanent high angle structure is added at the tunnel from the TBM trailing deck. This is because the conveyor is running without lapse so the material hugging must also be without lapse. This challenge does not occur at conveying angles up to about 30 ° as the contact and mere weight of the top belt stabilizes the bulk load and develops its internal friction. This also means that at high angles to approximately 30 °, GPS (gently pressed sandwich) type pressing rolls are not required and the mere top belt suffices.
The interim hugging is accomplished with a weighted blanket over the top belt for conveying angles of approximately 30 to 55° and torsionally sprung air plenums for incline angles above 55°. In either case, the interim hugging system is secured to the high angle structure of the TBM trailing deck and creates a smooth upper surface that the permanent GPS pressing rolls can roll over and onto the top belt as they assume the permanent hugging function. This series of six slides that depict adding the permanent conveyor structure as the TB advances, leaving the tunnel anchored hanging structure behind.
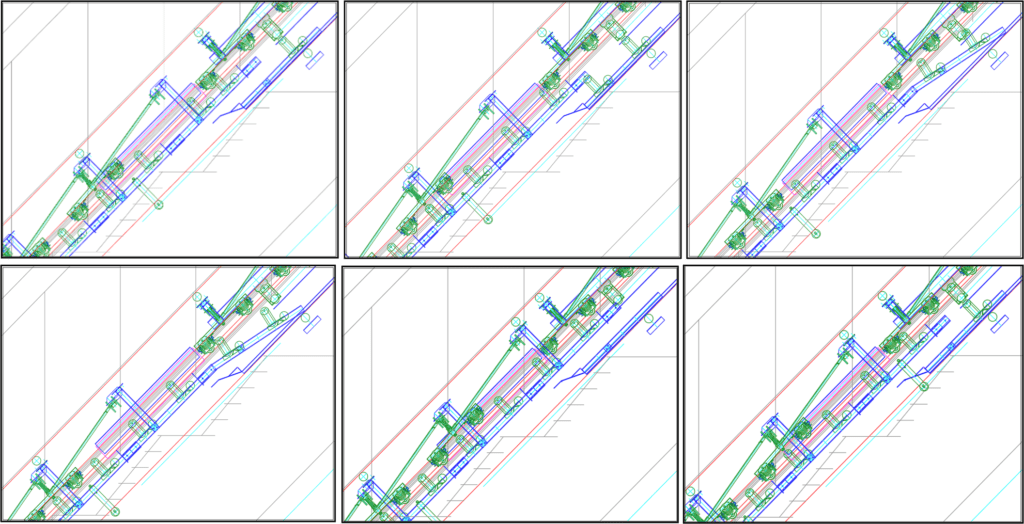
The invention promises to revolutionize haulage from high angle tunnel excavations affording all of the benefits of TBM trailing conveyors that were not previously available at high incline angles.