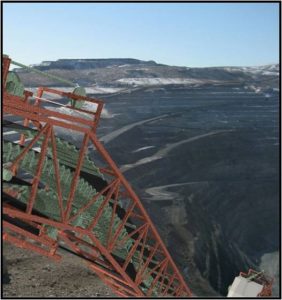
Various articles that announce high angle conveying from open pits as “innovative”, “next phase” and “new”, prove that not enough people in the industry are doing their research. This cost efficient method of conveying has been proven and available for over 30 years and remains ignored by the IPCC (in-pit crushing and conveying) equipment and systems providers. For a company like Dos Santos International, it is increasingly frustrating to see these articles make their way to publications as a new technology, when President and owner, Joseph Dos Santos has offered this option throughout his career. Joe is the inventor of the DSI Sandwich Belt High Angle Conveyor and has researched and spoken regularly on the subject of high angle conveying, and how it offers the vital and missing link to optimized IPCC systems.
HISTORY
Reduced energy consumption and environmental impact, with IPCC systems, was already realized in the 1970’s. With bulk material haulage limited to conventional open trough conveyors, this precluded the most direct path out of the open pit, requiring low angle spiral ramps and/or deep slots and/or tunnels through the pit high wall. These excavations, to accommodate the low angle limitations, represented undesirable impact on cost and on the environment increasing the amount of environmental disturbance for the amount of ore recovered. Against this backdrop, a major study in 1979 sought to develop high angle conveying systems that could continuously haul the mined bulk material directly out of the pit, along the high wall, “the shortest distance between the two end points.” Between 1979 and 1982 that study developed sandwich belt high angle conveying systems that utilized all conventional conveyor equipment, including smooth surfaced rubber belts that could be continuously scraped clean. These systems had all of the positive features of conventional conveyors, but overcame the angle limitation. By hugging the bulk material between two belts, the material’s internal friction could be developed to facilitate conveying at any high angle up to 90° (vertical).
After an intense testing period (about 1 year) on the first large scale prototype system, commercialization began in 1983 with the installation of a 60° incline system at a western USA coal mine, elevating 2000 t/h of coal to a train load out system. It did not take a long period of scrutiny and acceptance before this high angle conveyor found use in the most rugged requirements of an IPCC system. This was only the second commercial sale, and after more than 150 commercial installations, it remains arguably the most significant high conveying system.
In this case, a copper mine, already using pit perimeter crushing and conveying, decided to move their primary crusher deep into the pit and use a sandwich belt high angle conveying system to elevate the ore continuously, directly out of the pit, along the high wall to the pit perimeter where it then transferred to a conventional conveyor for the remaining haul to the plant. The system had significant features including 2000mm wide belts that elevated 250mm coarse ore, at 4000 t/h, over six 15 meter high benches for a total of 90 meters of lift. The system was able to reduce the truck haulage fleet by 10, 200 ton trucks realizing great cost savings, zero emission to the air, and greatly reduced traffic congestion in the pit. They system operated successfully until 2002 when the mine shut down.
SUITABILITY OF THE SANDWICH BELT HIGH ANGLE CONVEYOR
Suitability for IPCC systems has been demonstrated at all Dos Santos sandwich belt high angle conveyors with a number of units handling very large ore and rock at very high rates.
The most common concerns regarding sandwich belt high angle conveyor suitability for IPCC applications:
- Can they handle very high tonnage rates?
- Are they suitable for continuous operation 24/7?
- Can they handle large, heavy, primary crushed ore and waste rock?
The various installations answer these questions. Of these, the most important concern is third on the lists. The answer is that – large belts can handle large lumps, small belts can handle small lumps.
Figure 2 shows a comparison of sandwich belt cross-sections for widely varying belt widths. Clearly “large” lump size is relative. 350mm lumps are too large to handle at a sandwich belt of 1000 mm width, but not at a sandwich belt of 2600 mm width. Indeed, to have compatibility of belt width and material size we limit the material size with regards to the trough depth. For predominantly lumpy
material, less than 10% large lumps, we increase the size criteria to 125% of the trough depth. This is to limit the separation of the belts, preserving a good covering of the bulk material and positive contact at the edges of the sandwich.
Sandwich belt high angle conveyors can and have conveyed very large oversize material from the sandwich entrance to the discharge. At a muck handling system a 150 HP TBM cutter motor was unintentionally but successfully conveying from loading point to the discharge. There was some very minor damage, but the system continued to operate until a scheduled down time to make the minor repairs. It is not a question of what is the largest material that can be handled. The Dos Santos criteria are to determine the material size that should be handled for reliable, trouble free operation with minimal wear and tear.
The only IPCC application to date in a copper mine, shows that the 250mm lumps are easily handled at the 2000 mm wide belts.
Five years after start up, the system proved its worth:
- Reducing the truck fleet by 10.
- Precluding the need for 4 km of haulage ramps, 3.5 km of which would be of constant ascent.
- Saved $12 million USD per year.
Almost an IPCC application, another sandwich belt high angle conveyor elevates coarse (250 mm minus) gold ore from the primary jaw crusher to the next crushing stage. It is at the pit perimeter, not in the pit. Definitely and overreach on the lump size handled, this conveyor suffered some wear and tear consequences but remains in operation today more than 25 years later.
The vital elevating link of a self-unloading ship system, handles a variety of materials including 305 mm minus rock. The sandwich belt high angle conveyor lifts the material onto a boom conveyor that discharges the bulk cargo to shore. This system is right at the edge of the maximum lump criteria for occasionally lumpy material <10% lumps. Design reflected that, the very coarse rock material is one of several commodities transported, and
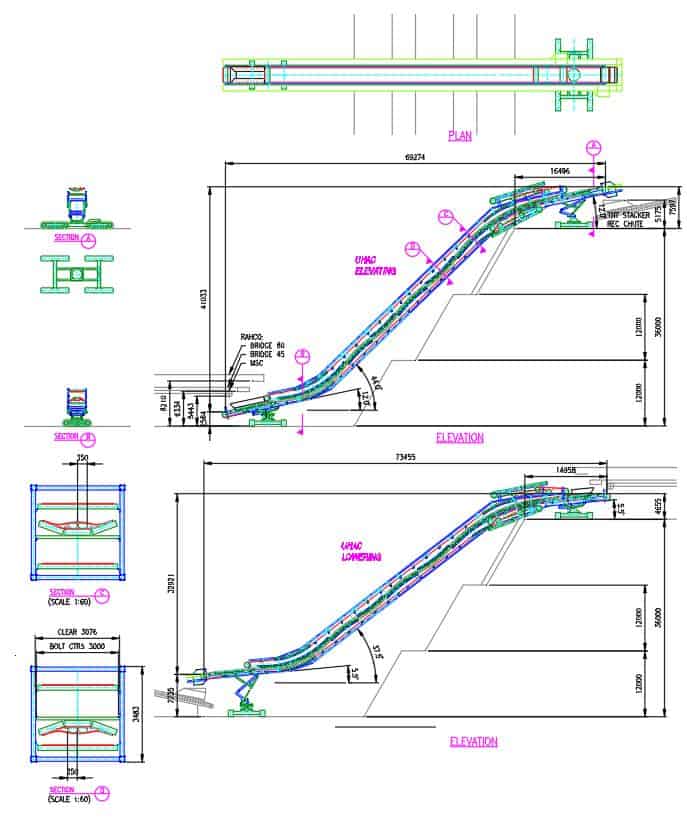
the unloading conveyors don’t operate continuously 24/7, rather there is much none-operating time at sea. This system replaced a massive apron type elevator that suffered very costly wear and tear.
Depicted in figures 3 and 4 the UHAC (universal high angle conveyor) is a prospective application in Western Australia. It is designed as the vital link to salvage an existing IPCC system that has proven sluggish due to its dependency on long, low angle conventional conveyors that link the IPCC system to the remote spoiling system. Operation of the present system proved impractical largely due to the extensive planning required, much non-productive movement, excavation and re-handling and grading work required to accommodate the present low angle link. Presently the system sits idle awaiting the vital link that will free the rigid interdependency of the in-pit system and the remote spoiling system.
The UHAC promises salvation, providing a compact mobile link, capable of elevating or lowering the primary crushed 350 mm minus waste rock at 8000 t/h. Designed with the emphasis on versatility the UHAC can operate in either direction (elevating or lowering the material) and at any level from tramming on grade to a 3×12 meter bench operation. The UHAC offers the vital versatile link for surface spoiling (elevating) or back filling of the mined out pit (lowering).
Clearly Dos Santos Sandwich Belt High Angle Conveyors are suitable for IPCC applications.
- They can handle very high conveying rates.
- They are suitable for continuous 24/7 operation.
- High tonnage requirements are handled by wide belts that can easily handle large, primary crushed material.
- Conscientious design will ensure long life with minimal maintenance required.
The system is proven commercially now for thirty five years with success in a significant IPCC system more than twenty five years ago.
Despite the compelling economics, mining operations have not taken full advantage of this technology, effectively foregoing a great potential for improved production and profits. End users have been disappointed by the large IPCC manufacturers who have failed to embrace the gift of a compact, versatile, vital link to any IPCC system. The industry continues to struggle with the use of conventional conveyor systems of limited flexibility requiring excessive maneuvering time, excessive excavation, fill and re-handling in order to accommodate the low angle limitations. The current alternative to conveyors is the fall back position of using 300-ton haul trucks at great operating cost. With such clear evidence of the suitability and benefits of sandwich belt high angle conveyors, it remains frustrating that mine owner and operators continue to explore what is marketed as new innovation, instead of what’s been proven for years.
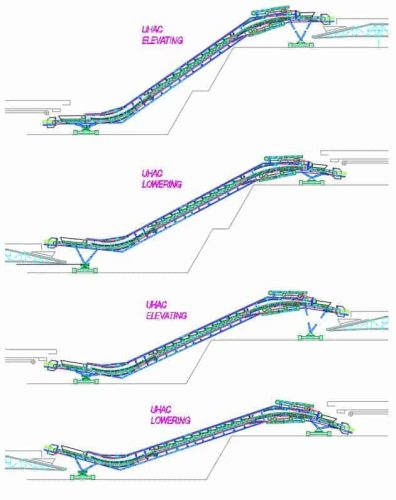